Hardly anything is more resilient to wear and tear than PCD milling inserts, which are crafted from polycrystalline diamond. This composite works well with aluminum, plastics, and other material varieties, making it a popular choice in various machining tasks.
A plethora of choices await when exploring PCD milling inserts. Depending on the project’s specific requirements, the right size, shape, and grade can be found. K10, K20, and K30 come most frequently to the table. Their applications include machining aluminum, plastics and composites respectively. If further wear resistance is desired, K10 and K20 inserts are available featuring a TiAlN (titanium aluminum nitride) coating.
For enhancing productivity in face and copy milling, PCD milling inserts are an ideal choice. Mount the insert in a milling cutter body and spin it at a fast rate. The cutting edge of the insert will make contact with the workpiece, chipping away material to craft the desired shape.
The CNC spindle acts as the platform whereupon the tool holder is fastened, presenting the insert adjacent to the surface of the workpiece. By turning the spindle slowly, pockets of material are gradually whittled away until the insert has achieved the specified shape. This practice known as copy milling.
PCD milling inserts are renowned for their impressive durability and are versatile enough to be used when cutting a variety of materials. K10 and K20 inserts have been developed specifically for machining aluminum and plastics, and K30 is mainly used for milling composite surfaces. Each of these grades can be enhanced with an extra layer of TiAlN coating to further protect against wear.
Related Product
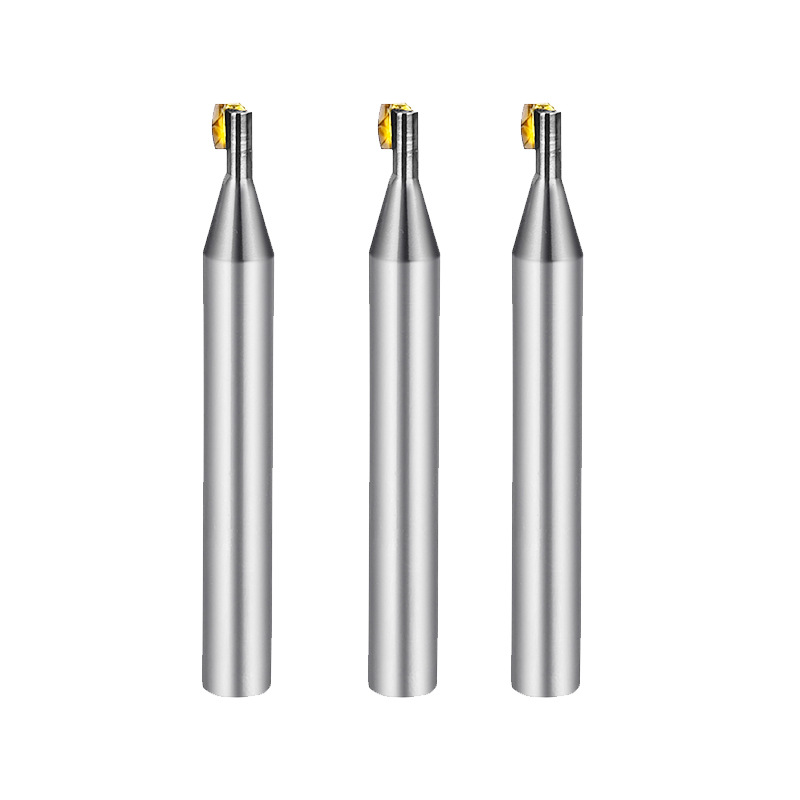
Diamond Turning Tools Outer Jewelry R Cutter
Product Information Origin Tianjing, China Material Tungsten Steel Brand Msk Type Half Round Key Milling Cutter Product Name Single Crystal Diamond Side Edge Arc Milling Cut […]
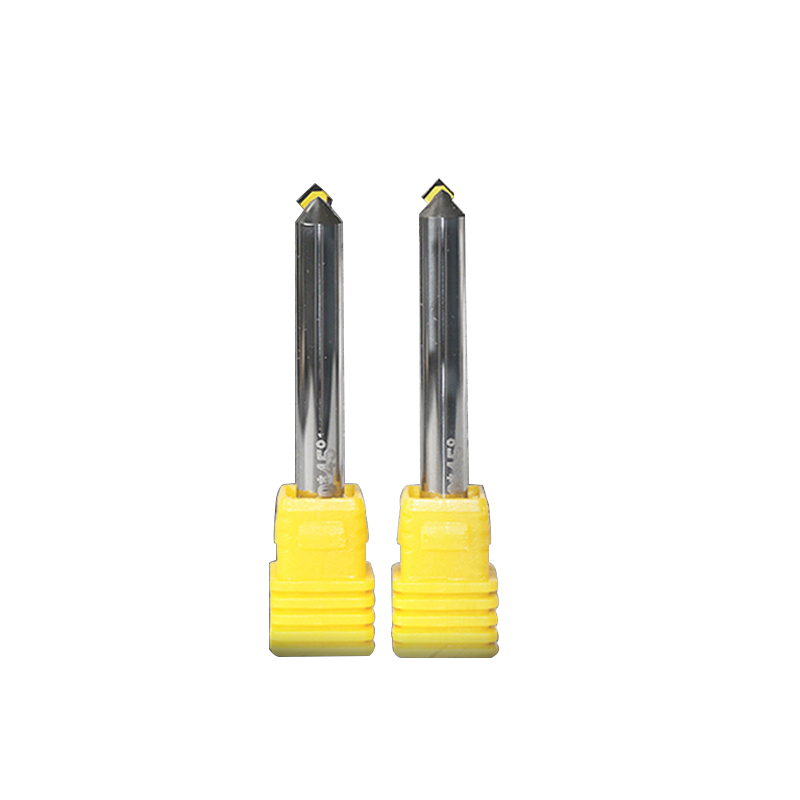
MCD Polishing Cutter for Gold Silver
Product Information Origin Tianjing, China Whether To Coat Uncoated Brand MSK Unit Weight 0.3kg Tool material Tungsten steel bar imported from Germany Product Size Shank Dia […]
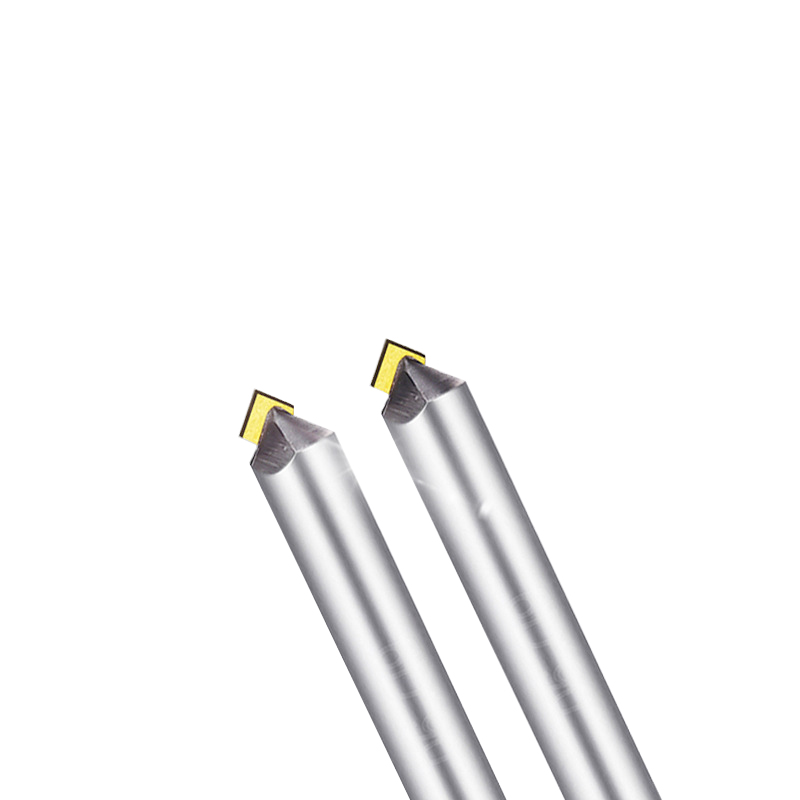
Lathe Bits MCD High Gloss Chamfer Tool
Product Information Origin Tianjing, China Cutting Edge Form Straight Edge Brand MSK Material Single Crystal Diamond Chamfer Angle 30°-180° Type Angle Milling Cutter Minimum […]
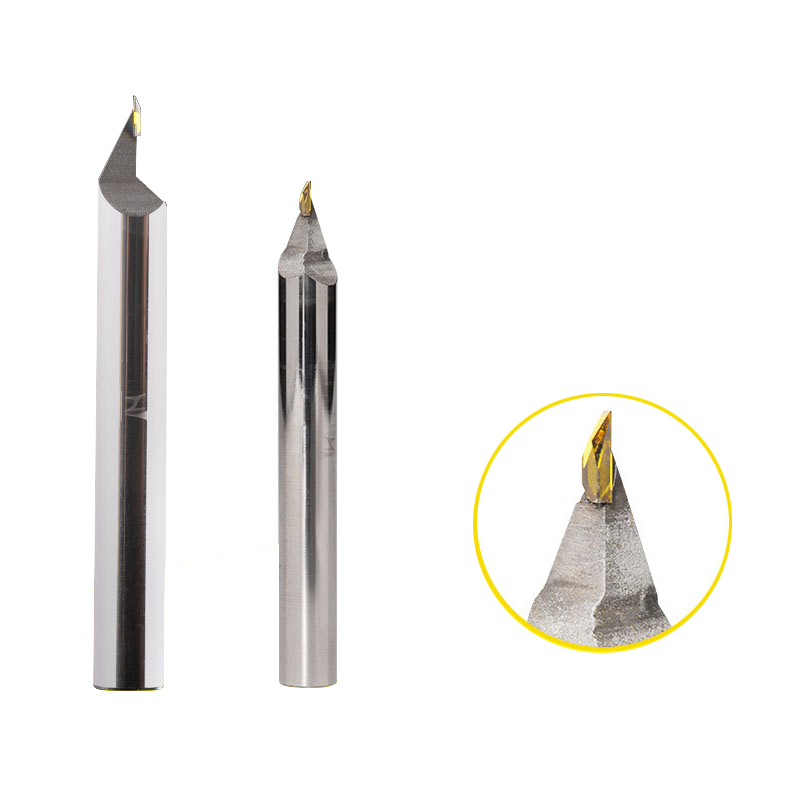
CVD/PVD/MCD Gold Jewelry Diamond Engraving Cutter
Parameter Product Name Single Crystal Diamond Carving Cutter Rotating Speed 10000-30000r/min Tool Nose Width 0.1-6.0mm Feed 1500-5000mm/min Blade Material Single Crystal Dia […]
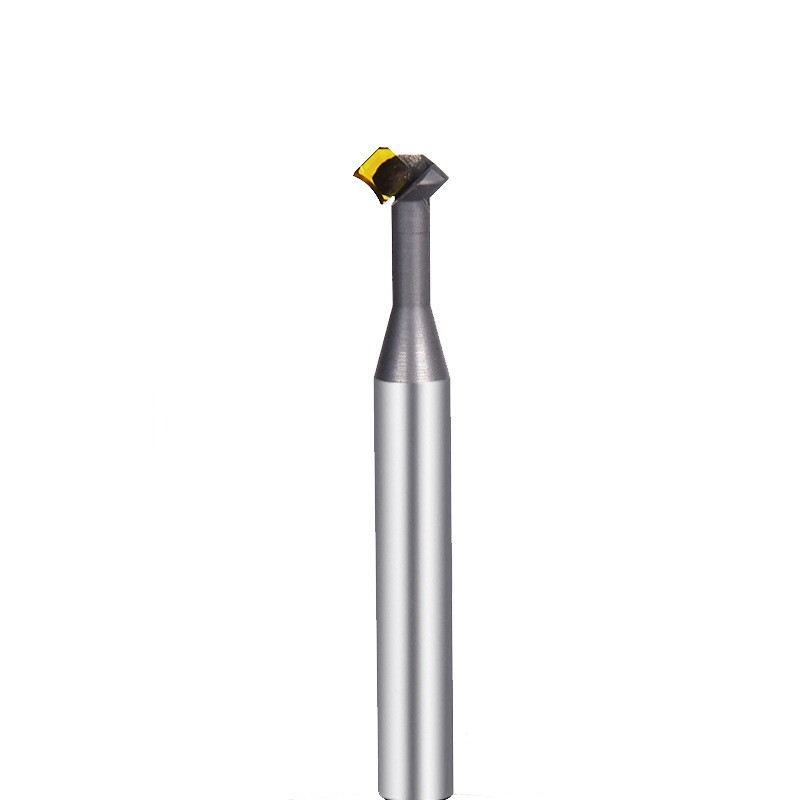
MCD Turning Tool Mirrow Finish R Cutter
Product Information Product Name Single Crystal Diamond Lower Chamfering Inner R Cutter Brand MSK Handle Material Tungsten Steel Blade Material Customized Pcd, Single Crysta […]
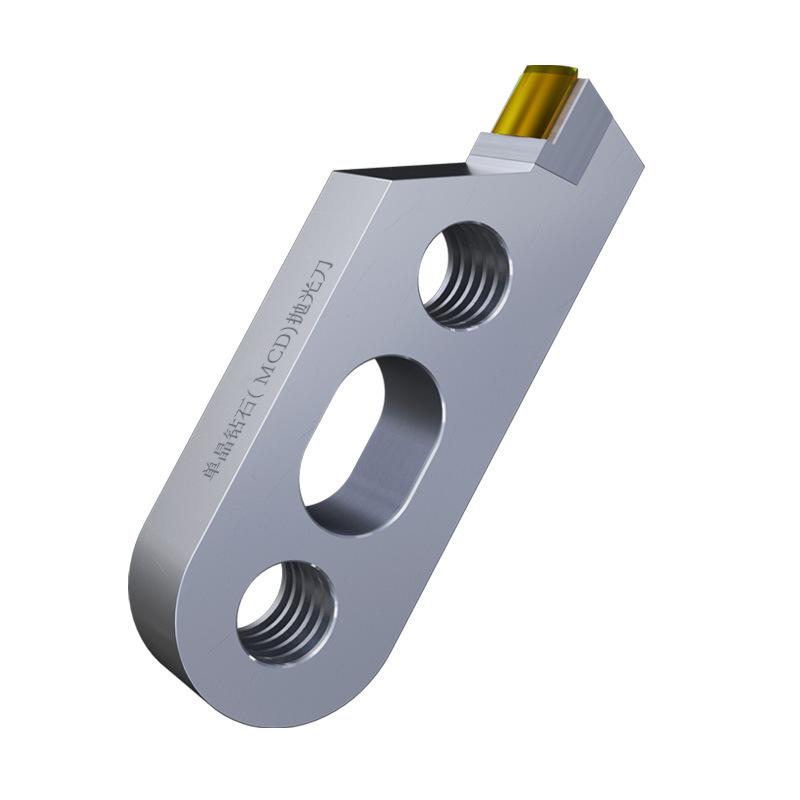
Single Crystal Diamond Polishing Cutter
Origin Tianjing, China Shank Diameter 6 (mm) Brand MSK Blade Change Method The Diamond Is Welded To The Cutter Body As A Whole Material Single Crystal Diamond (MCD) Scope Of […]
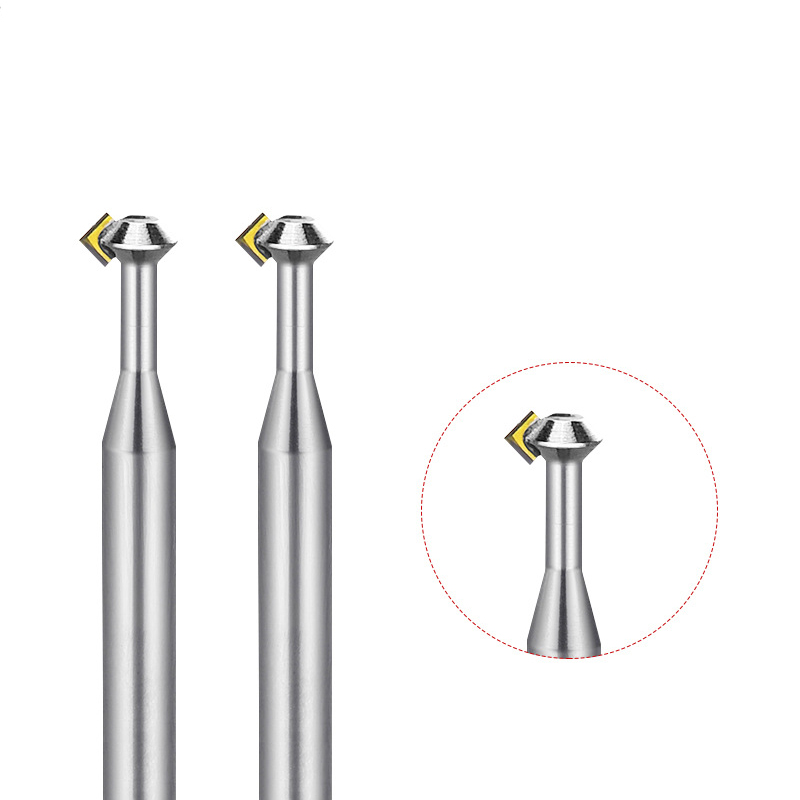
MCD High Gloss Chamfer Cutter For Gold
Product Information Origin Tianjing, China Type Flat Milling Cutter Brand Msk Whether To Coat Uncoated Series Cutter Milling Cutter Processing Range Clocks And Watches, Copp […]
Post time: 2023-06-22