For many applications in crafting, creating, and constructing, diamond core cutters are essential tools. However, over time, their performance may begin to degrade. To restore and improve the process of diamond core cutting, the method of core boring diamond cutter refurbishing is often employed. This method is used to sharpen diamond cutters by creating a modified shape and size according to the material at hand – be it concrete, metal, or stone. This specialized type of tool is valuable in transforming a variety of materials for use in various industrial tasks, from construction to manufacturing.
When core boring diamond cutters have lost their effectiveness, they must undergo refurbishment to return them to peak performance. Restoring these instruments towards like-new condition necessitates certain skills, tools, and familiarity of their design. Refurbishing core boring diamond cutters includes a multi-step process tailored to the specific cutter being revitalized.
After an extensive inspection to evaluate the condition of the core boring diamond cutter, any signs of degradation, such as blunting, chipping or corrosion, should be dealt with swiftly. Following this essential check-up the refurbishment can begin. It is vital that this preparatory stage is thorough in order to ensure a successful and lasting result.
A technician should select the appropriate cleaning agents for the kind of material from which the cutter is constructed; possible options consist of solvent, abrasive, and lubricating agents. After the cutter is pristine, it’s then time to refurbish it. To do this, smooth out any rough edges or burrs via sanding or grinding. Lastly, apply a coating to protect the cutter from oxidation.
With the next step, it’s all about getting the cutting surfaces sharpened. A technician must deploy specialized tools for grinding and polishing, being mindful not to grind the surfaces too harshly or create an uneven finish, both of which can reduce cutter performance significantly. Striking the delicate balance between too much and too little is vital for optimal results.
Once the sprucing-up is complete, the technician can check the cutter to make sure it functions correctly. Additionally, they should look for any wear or tear, in addition to verifying that the cutting faces are uniformly honed. If there are any issues, appropriate measures can be taken to address them.
A professional technician is vital to restore core cutting diamond cutters back to optimal operation, for a refurbishing process that requires exceptional tools and practices. Through use of the directions shared herein, you can ensure an enduring performance from your core boring diamond cutters – as good as new.
Refurbishing old diamond cutters can be made easier with core boring. By drilling and boring holes in concrete or metal surfaces, accuracy and durability can be greatly improved. The precise nature of core boring makes it ideal for cutting diamonds, allowing for precise and detailed results.
For projects requiring a hole of specific size or depth, core boring provides an effective solution. This process utilizes a motor-powered drill equipped with diamond cutting tools to precisely carve the necessary hole. The speed of the drill may be adjusted to ensure optimal control over the production, allowing for tailored cutting sizes and depths with each application.
Once the initial excavation has been accomplished, diamond-tipped cutting tools are then employed to give the internal face of the opening a smooth finish. The use of diamond decked instruments allows for a sharp and precise edge to form. These cutting tool can be appropriately adjusted in order to generate wider or thinner holes depending on the desired design.
After our work with the drilling and cutting is finished, we move on to the diamond cutting tools for a refined look. We use a diamond polishing wheel, which glides over the space for a sleek finish. Thanks to this process, any irregularities or scratches are carefully buffed out – leaving a smooth and perfect surface.
Last but not least, the diamond-edged tools are needed to form a novel surface on the hole. This is done through a diamond grinding wheel, which helps give the whole a brilliant new finish with raised accuracy and durability. The use of the grinding wheel also allows for customizable hole sizes and shapes.
Finessing diamonds to perfection, core boring is a precise way to redevelop ageing diamond cutters and create new surfaces with surpassing accuracy and resilience. To reach this aim, special diamond cutting tools and machines must be acquired, as well as a diamond polishing wheel and a diamond grinding wheel. This process provides the capability to not just flawlessly cut diamonds but also design novel shapes and enlarge the existing holes.
Related Product
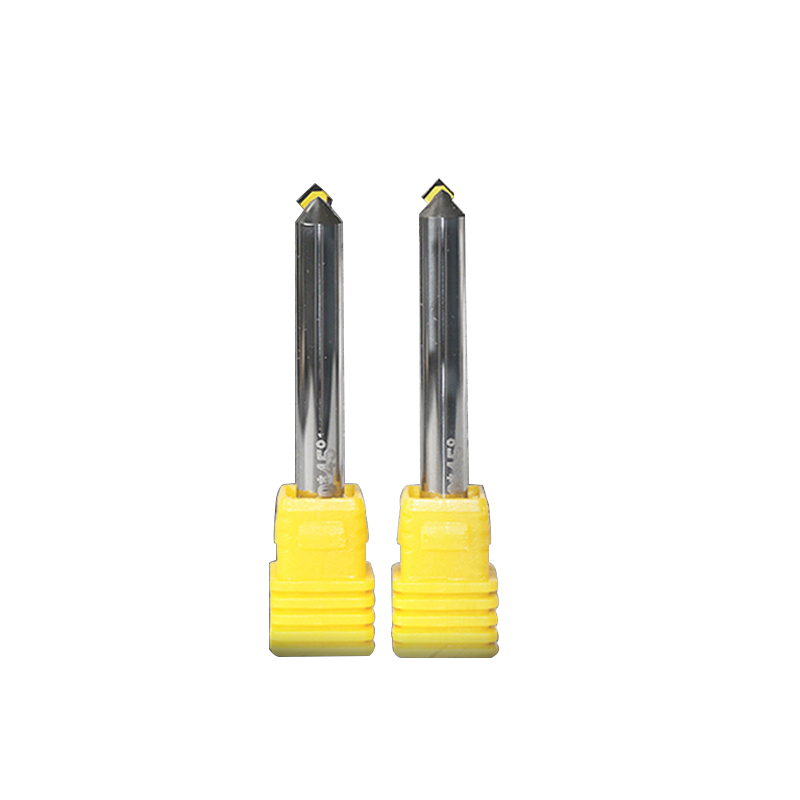
MCD Polishing Cutter for Gold Silver
Product Information Origin Tianjing, China Whether To Coat Uncoated Brand MSK Unit Weight 0.3kg Tool material Tungsten steel bar imported from Germany Product Size Shank Dia […]
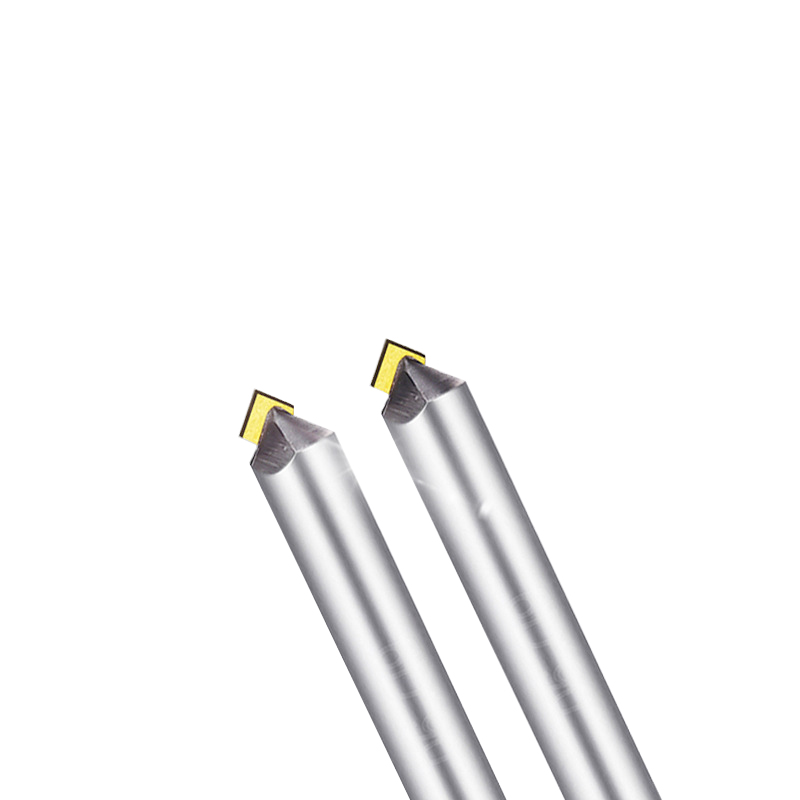
Lathe Bits MCD High Gloss Chamfer Tool
Product Information Origin Tianjing, China Cutting Edge Form Straight Edge Brand MSK Material Single Crystal Diamond Chamfer Angle 30°-180° Type Angle Milling Cutter Minimum […]
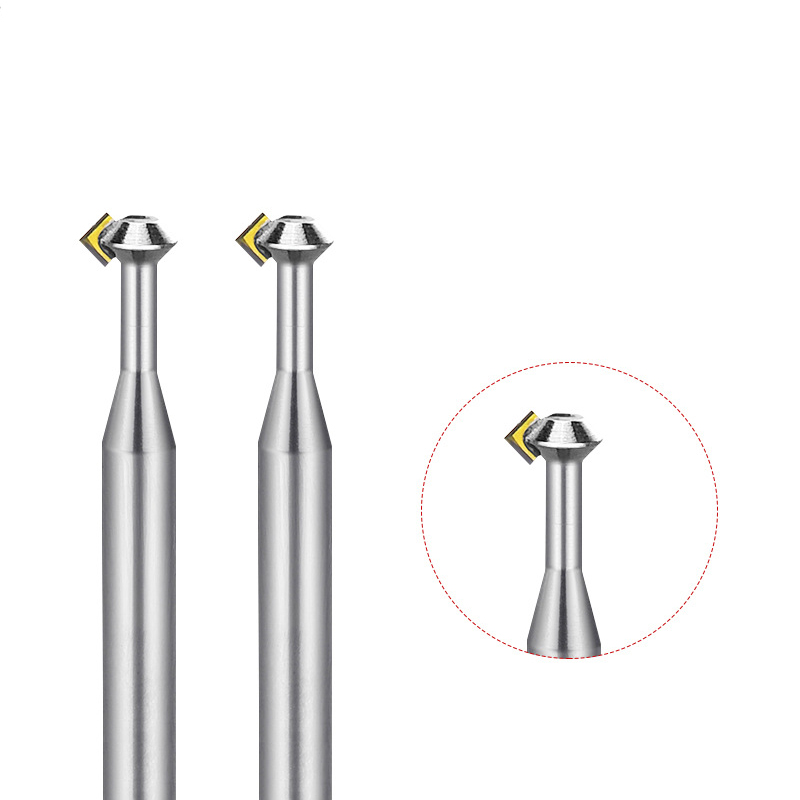
MCD High Gloss Chamfer Cutter For Gold
Product Information Origin Tianjing, China Type Flat Milling Cutter Brand Msk Whether To Coat Uncoated Series Cutter Milling Cutter Processing Range Clocks And Watches, Copp […]
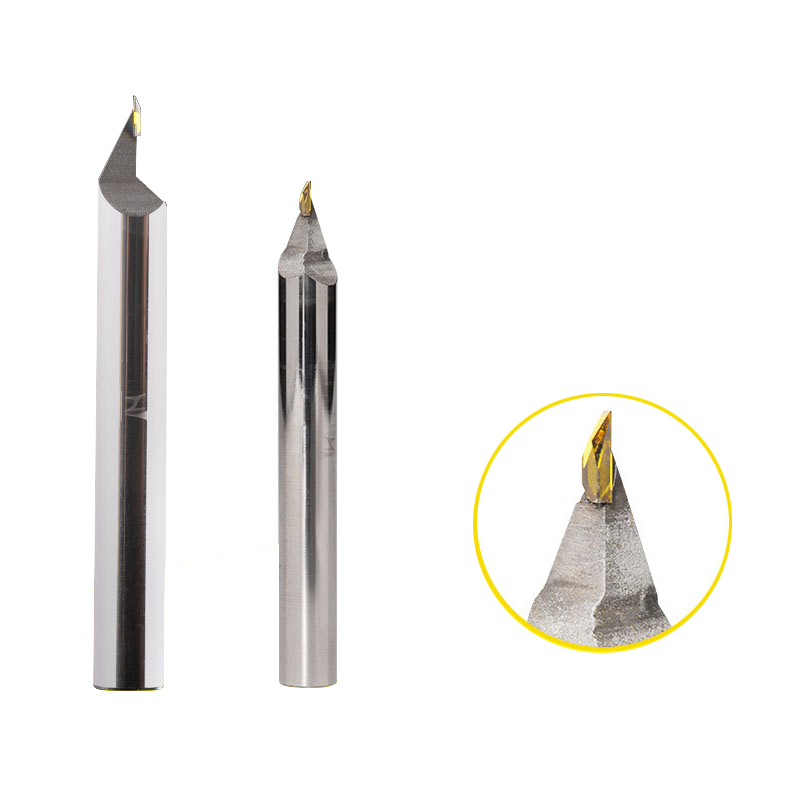
CVD/PVD/MCD Gold Jewelry Diamond Engraving Cutter
Parameter Product Name Single Crystal Diamond Carving Cutter Rotating Speed 10000-30000r/min Tool Nose Width 0.1-6.0mm Feed 1500-5000mm/min Blade Material Single Crystal Dia […]
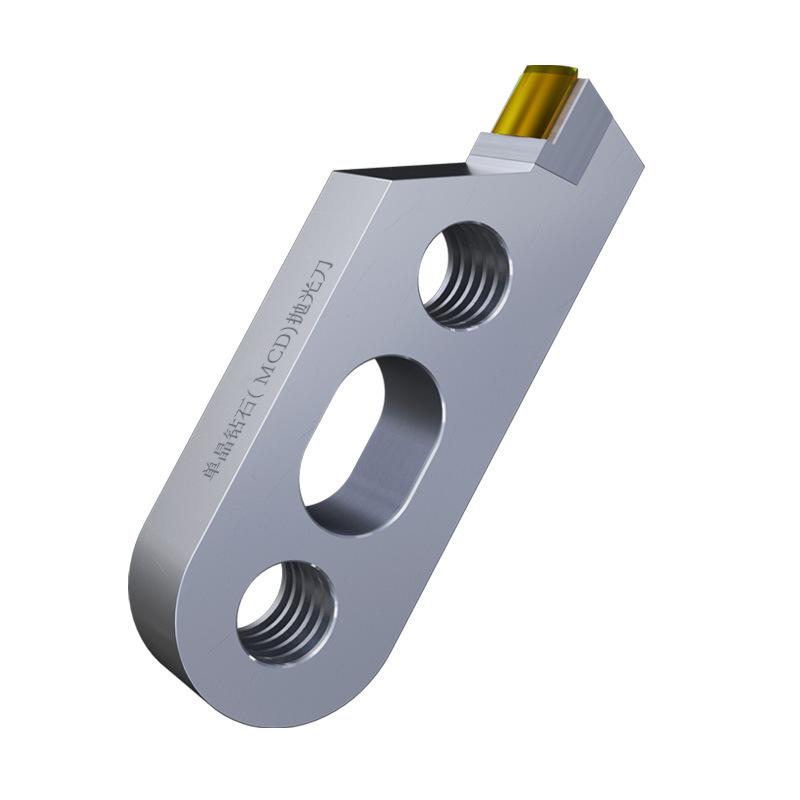
Single Crystal Diamond Polishing Cutter
Origin Tianjing, China Shank Diameter 6 (mm) Brand MSK Blade Change Method The Diamond Is Welded To The Cutter Body As A Whole Material Single Crystal Diamond (MCD) Scope Of […]
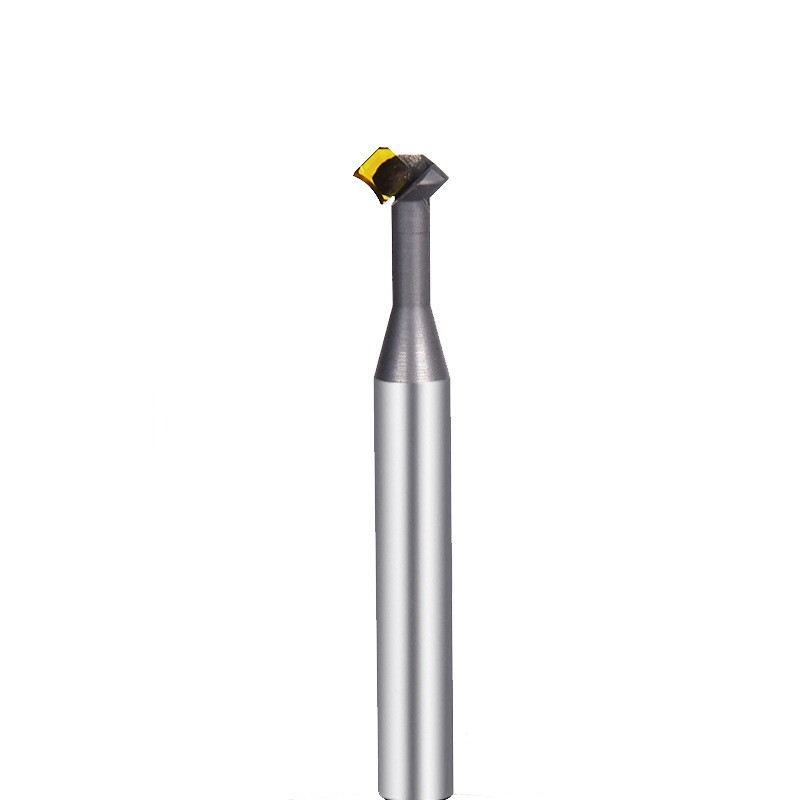
MCD Turning Tool Mirrow Finish R Cutter
Product Information Product Name Single Crystal Diamond Lower Chamfering Inner R Cutter Brand MSK Handle Material Tungsten Steel Blade Material Customized Pcd, Single Crysta […]
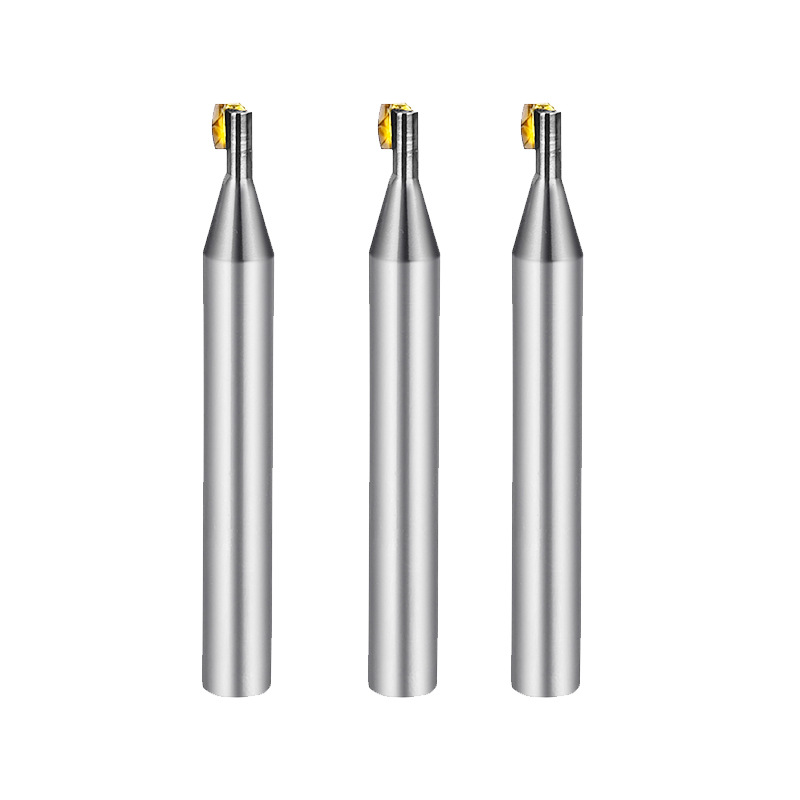
Diamond Turning Tools Outer Jewelry R Cutter
Product Information Origin Tianjing, China Material Tungsten Steel Brand Msk Type Half Round Key Milling Cutter Product Name Single Crystal Diamond Side Edge Arc Milling Cut […]
Post time: 2023-07-18